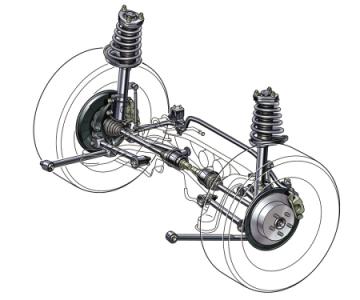
懸架是車架與車橋或承載式車身與車輪之間的一切傳力連接裝置的總稱,其性能直接影響整車的安全性、可靠性。后懸架系統(tǒng)是否滿足產品的設計需要,對整車的性能起到關鍵作用。有限元分析技術為快速經濟地實現(xiàn)這樣的設計目標提供了可能。對于復雜的結構件,在汽車結構設計的初始階段引入有限元模擬技術,而不再是僅憑經驗來設計或修改結構,減少了昂貴的樣件生產和測試的次數,大大縮短設計周期和節(jié)省產品開發(fā)成本。某工程車斷開式后懸架系統(tǒng)在結構設計的概念和圖紙設計階段,借助于有限元技術通過對兩個設計方案計算結果的分析比較,選出滿足結構強度和輕量化并舉的最佳懸架系統(tǒng)結構,從而既經濟又快速地實現(xiàn)工程實際目標。
最為流行的CAE分析軟件之一,HyperWorks因其擁有其它分析軟件所無法比擬的前、后處理功能,越來越廣泛的被運用于工業(yè)領域。首先在有限元軟件Hypermesh的前處理平臺上,建立后懸架系統(tǒng)完整的三維實體模型。后懸架系統(tǒng)包括車架,平衡軸,平衡軸支架,鑄造橫梁,橫梁加強板及下連接板,由于后懸架系統(tǒng)空間布局的復雜性,建模時要注意局部坐標和整體坐標的調整,這樣能夠大大減小確定各部件總成相對位置和坐標的工作量。兩個后懸架系統(tǒng)的區(qū)別見圖,為了減少平衡軸支架對安裝孔的干涉,后懸架系統(tǒng)的平衡軸支架增加了寬度。
在將兩個實際后懸架系統(tǒng)的三維實體模型轉化為有限元計算模型時,對車架進行了一些簡化處理,以降低有限元計算模型中的單元數。車架的骨架比較大,在總的外形尺寸保持不變的情況下,縮短車架長度,并對兩端進行約束。車架,橫梁加強板及下連接板,在計算模型中利用四邊形的殼單元模擬,大小控制在6mm。其他比較厚重的結構承載件則全部采用四面體的實體單元,大小控制在5mm。后懸架系統(tǒng)各結構件的材料選用見表。在靜載條件下計算后懸架系統(tǒng)的變形及其應力分布時,是相對于車輛的靜平衡位置,為了突出后懸架系統(tǒng)本身的變形狀況,在計算模型中,將簡化車架端面的所有自由度加以約束,以限制后懸架系統(tǒng)的剛體位移。后懸架系統(tǒng)承受的載荷,可以分為車輛動力裝置作用在平衡軸支架下端連接孔的作用力與車輪對平衡軸的重力載荷。車輛動力裝置對懸架系統(tǒng)產生的載荷平均分布在平衡軸支架下端的連接孔上。車輪重力靜載荷均勻分布在其平衡軸的四段承載面上。
在設定的后懸架系統(tǒng)有限元計算模型的邊界條件下,計算靜力載荷作用時后懸架系統(tǒng)的應力和位移分布狀態(tài),具體見圖,位移均發(fā)生在平衡軸外端面,位移小于0.5mm。后懸架系統(tǒng)的最大應力為267MPa,最大應力點位于平衡軸與平衡軸支架的上接觸面,如圖所示;后懸架系統(tǒng)的最大應力為271.6MPa,最大應力點位于平衡軸與平衡軸支架的下接觸面處,如圖所示。同時關注鑄造橫梁,平衡軸支架及平衡軸的應力分布情況,計算結果見表。從后懸架系統(tǒng)及各個結構件的應力分布狀況可以看出,結構的應力值顯著小于材料的屈服強度,且安全系數均大于1,說明兩個后懸架系統(tǒng)及相應結構件的強度和剛度完全能達到設計要求,且后懸架系統(tǒng)的安全系數相對較高。在滿足結構強度的要求下,輕量化的需求也是日益受到關注,而后懸架系統(tǒng)的質量較后者輕。通過對兩個設計方案計算結果的分析比較,后懸架系統(tǒng)成為滿足結構強度和輕量化要求下的較優(yōu)結構。
(1)兩種后懸架系統(tǒng)及各結構件的強度和剛度完全滿足設計要求,且后懸架系統(tǒng)的安全系數相對較高。(2)比較兩種后懸架系統(tǒng)的質量,后懸架系統(tǒng)的質量較后者輕6kg。(3)通過對兩個設計方案計算結果的分析比較,后懸架系統(tǒng)為滿足結構強度和輕量化要求下的較優(yōu)結構。
專業(yè)從事機械產品設計│有限元分析│強度分析│結構優(yōu)化│技術服務與解決方案
杭州那泰科技有限公司
本文出自杭州那泰科技有限公司jjycrms.com.cn,轉載請注明出處和相關鏈接!