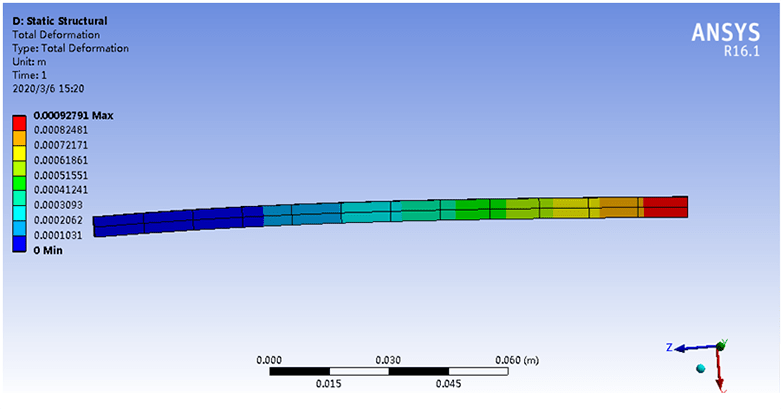
管道運(yùn)輸是輸送石油和天然氣等產(chǎn)品的安全運(yùn)輸方式,我國長輸油氣管道總長度在2014年已達(dá)12×E4 km,其中運(yùn)行時(shí)間在20年以上的占62%。由于老化和環(huán)境因素引起的腐蝕缺陷會(huì)降低管道的強(qiáng)度,減小其抗疲勞能力,造成管道局部屈曲、泄漏甚至爆破。目前,腐蝕缺陷已成為埋地油氣管道失效的主要原因,據(jù)統(tǒng)計(jì)因腐蝕缺陷導(dǎo)致管道破壞進(jìn)而發(fā)生的事故約占事故總數(shù)的50%左右。因此,對埋地油氣管道進(jìn)行定期檢測和管道剩余強(qiáng)度評(píng)估,建立高可靠度的管線剩余強(qiáng)度分析方法,對管道的安全性評(píng)價(jià)非常重要。
從20世紀(jì)60年代初開始,國外學(xué)者對管道剩余強(qiáng)度評(píng)價(jià)方法進(jìn)行了研究。例如,美國機(jī)械工程師協(xié)會(huì)根據(jù)半經(jīng)驗(yàn)斷裂力學(xué)公式提出了ASME B31G—2009準(zhǔn)則;英國燃?xì)夤竞团餐?jí)社共同完成了DNV。遥校疲保埃睒(biāo)準(zhǔn);美國Battlle實(shí)驗(yàn)室開發(fā)了PCORRC方法。我國也制定了SY/T6151—1995、SY/T。叮矗罚—2000、SY/T。保埃埃矗—2003等標(biāo)準(zhǔn)。20世紀(jì)90年代中期,B.Chouchaoui等首先提出了彈塑性有限元分析方法,隨著計(jì)算機(jī)技術(shù)的發(fā)展和有限元理論的不斷成熟,以有限元模擬為主、試驗(yàn)為輔的腐蝕管道研究方法被廣泛采用,并取得了豐碩成果。有限元模擬方法可以根據(jù)管道缺陷的實(shí)際形狀進(jìn)行建模,并且考慮管道材料的可塑性、應(yīng)力強(qiáng)化、大變形和大應(yīng)變等非線性因素。
國內(nèi)外的很多學(xué)者主要應(yīng)用有限元法評(píng)定平底缺陷腐蝕管道的剩余強(qiáng)度和剩余壽命,但是模擬的缺陷形狀相對單一,對橢球形等形狀缺陷進(jìn)行的研究相對較少。筆者借助大型有限元分析軟件ANSYS,采用幾何非線性和材料非線性有限元方法,針對我國某成品油管道檢測出的兩個(gè)缺陷,建立了橢球形缺陷管道模型,并計(jì)算了應(yīng)力狀態(tài),同時(shí),基于彈性極限準(zhǔn)則和塑性極限狀態(tài)失效準(zhǔn)則,在已知腐蝕速率的情況下,對腐蝕管線的剩余壽命進(jìn)行了預(yù)測。
某長輸成品油管道1995年10月投產(chǎn),至今已經(jīng)運(yùn)行近20年。管材為API。兀担蹭,管道直徑為377mm,壁厚為6mm,最小屈服強(qiáng)度為360MPa,抗拉強(qiáng)度為528MPa。從《機(jī)械設(shè)計(jì)手冊》查得,材料的彈性模量E=210000MPa,泊松比υ=0.3,設(shè)計(jì)壓力和最大允許操作壓力均為6.0MPa。在管道內(nèi)檢測時(shí)發(fā)現(xiàn)了多個(gè)缺陷,對其中的兩個(gè)缺陷進(jìn)行了開挖驗(yàn)證。驗(yàn)證結(jié)果表明,內(nèi)檢測尺寸較為準(zhǔn)確。兩個(gè)腐蝕缺陷的詳細(xì)尺寸見表1,F(xiàn)以2#腐蝕缺陷為例,介紹建模及求解過程。
外腐蝕管道有限元模型的建立在有限元分析過程中,為了能找到一定的外腐蝕安全評(píng)估規(guī)律,可將腐蝕寬度較小的缺陷簡化為形狀規(guī)則的模型,即同時(shí)對稱于通過管道軸線的平面和垂直于管道軸線的平面的橢球模型。為了節(jié)省計(jì)算資源,在分析過程中。保吹墓艿滥P汀榱讼吔缧(yīng),根據(jù)圣維南原理,管道長度。保埃埃埃恚恚ù笥诠軓降模脖叮。在建立幾何模型時(shí),對管道模型與橢球模型進(jìn)行布爾減法運(yùn)算,即可得到橢球形缺陷。
專業(yè)從事機(jī)械產(chǎn)品設(shè)計(jì)│有限元分析│CAE分析│結(jié)構(gòu)優(yōu)化│技術(shù)服務(wù)與解決方案
杭州那泰科技有限公司
本文出自杭州那泰科技有限公司jjycrms.com.cn,轉(zhuǎn)載請注明出處和相關(guān)鏈接!